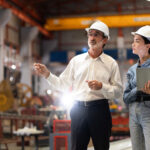
How to Prepare for an Inspection
October 25, 2023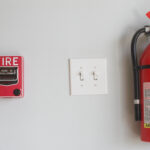
Portable Fire Extinguishers: Training and Inspection Requirements
October 25, 2023Four Flaws In Injury Prevention Programs
Sustaining a low or injury-free workplace requires strong leadership and constant attention. The most recent data on workplace injuries and illnesses (Bureau of Labor Statistics, 2021) showed an increase in the number of fatal and nonfatal injuries. Particularly disturbing was the fatal occupational injury rate of 3.6, which represents the highest annual rate recorded since 2016. In 2021, 5,190 workers suffered fatal work injuries, equating to one worker death in the U.S. every 101 minutes. Further, the days away, transferred, or restricted (DART) rate for more serious nonfatal injuries and illnesses has increased. According to the National Safety Council (NSC), the economic costs of work-related deaths and injuries is $167 billion and days lost due to injuries in 2021 totaled 70,000,000.
Despite significant improvements in safety practices, employers are struggling with the ability to prevent the most serious and costly workplace injuries. Here are four common weaknesses in injury prevention programs:
- Underestimating moderately hazardous environmentsWhile the possibility of an accident is always present, the probability of an injury occurring is dependent on environmental factors and safety behaviors. A recent study by Waterloo University researchers found that workers are more likely to adjust the degree to which they engage in safety behaviors according to the hazardousness of the situation. “Within highly hazardous environments, individuals typically exhibit a high degree of safety behaviors, as these environments are characterized by rules, procedures, and physical barriers to ensure maximum safety behavior. In contrast, work environments with relatively few hazards require little (if any) effort to be allocated to safety behaviors. Yet, many work situations fall between these extremes. We argue that moderately hazardous environments are particularly challenging when it comes to matching safety behaviors to the demands of the situation.”
The researchers argue relatively small increases in hazardousness, require a sharp, non-linear increase in safety behaviors, but most workers will not increase safety behaviors to the degree necessary. Instead, the typical response to increased hazardousness is likely to be a proportional increase in safety behaviors. The team conducted four studies and concluded that under moderately dangerous conditions, participants exhibited only a “moderate degree” of safe behaviors. Despite being aware of the hazards in the moderately dangerous conditions, the participants underallocated time and effort needed to work safely. As a result, accidents are more likely to occur in moderately dangerous work settings.
Employers need to recognize that workers will adjust safety behaviors based on their perception of what is needed to avoid accidents. It’s critical not only to train workers on how to perform safety behaviors but also when to apply these behaviors.
- Failure to assess the exposures that have SIF potentialOSHA recordables and safety audits can play an important role in identifying frequent exposures and preventive actions but often fall short of identifying serious injury and fatality (SIF) threats. Research and client experience from the global consulting firm, DEKRA Organizational Safety and Reliability, shows that 25 percent of OSHA recordable events have realistic SIF exposure potential. Since fatal and life-altering incidents rarely happen and are often viewed as an anomaly, identifying the potential of a less serious injury to become an SIF is challenging.
DEKRA notes, “This means that just a single factor could have easily and realistically changed, leading to a completely different and more severe outcome.” This could be a fatality or life-altering injury. Consider the situation where a worker trips on the carpet, falls and fractures a wrist. Realistically, this is a probable worse-case outcome. But if the worker fell from a platform and suffered the same injury, there are worse potential outcomes including a life-altering spinal cord injury or even death. By monitoring and recording SIF potential events, as well as actual SIFs, there is a basis for assessing progress and detecting risks.
- Acceptance of normalization of devianceNormalization of deviance is defined as the process where a clearly unsafe practice becomes considered normal if it does not immediately cause a catastrophe. The original example was the space shuttle Challenger disaster in 1986. Although NASA was aware of the problems that led to the catastrophe, nothing was done to correct the issues because previous shuttle missions had lifted off without negative consequences. Today, distracted driving is an obvious example.
While it’s often cited as an issue that affects safety in high-risk organizations, it’s also applicable to individual workers. And it can be insidious – workers who deviate from the norm often aren’t aware of their unsafe behavior. Even though the company has a robust ladder safety program and trains workers well, a worker opts to use a nearby ladder that’s too short for the job and steps on the top cap to reach the shelf, although it’s risky. Since there was no injury, they are likely to repeat the behavior time and time again. Eventually, they will not even think about it as unsafe and will stop seeing the action as deviant. Working this way becomes accepted practice, and the deviation becomes normal practice, although it could lead to a serious injury.
To stop the unsafe behavior will require an intervention by a supervisor, a proactive co-worker, a near miss, or worse, a fall resulting in an injury. When injured employees are asked why they chose to do something different when they know the safe way of behaving, a common answer is, “I didn’t think I would get hurt.”
There is a difference between knowledge and awareness. Awareness requires an emotional connection and personal commitment that acknowledges what could go wrong and compels them to comply with expected safe work practices. Administrative controls and robust training are important, but not enough. A strong safety culture coupled with powerful, salient reminders of risk is the best way to foster awareness and break the risk-taking cycle.
- Lack of enforcement by supervisors, upper management commitmentThe absence of and inappropriate use of personal protective equipment (PPE) are major causes of fatal and nonfatal injuries at construction workplaces. A recent study, PPE non-compliance among construction workers: An assessment of contributing factors utilizing fuzzy theory, identified 16 factors that contribute to PPE noncompliance. While many past studies have focused on workers’ complaints about fit and comfort, making jobs more difficult, or beliefs it’s unnecessary, this study concludes that workers cannot be blamed for not using PPE. It found that the top contributing factor is lack of enforcement by supervisors, followed by lack of consistent upper management support, lack of training, and lack of PPE availability and accessibility. It did, however, acknowledge that firm size contributes to a lack of safety rules and policies as well as a lack of PPE availability and accessibility because smaller construction firms have limited resources to create and maintain adequate safety and health policies.
Supervisors may tolerate PPE non-compliance as they try to maintain good relationships with workers to complete projects on time. Training supervisors on safety coaching and encouraging, measuring, and monitoring frontline supervisor accountability can help them balance safety and productivity. According to the authors, “If you provide workers with the required training, the upper management commitment to safety is there, and there are supervisors who really care and enforce the safety regulations, PPE noncompliance will be much less than what we see today.”
For more information, schedule a meeting with one of our professionals today.