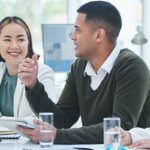
Financial Planning Support for All Employees
October 23, 2023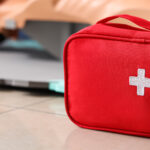
Four Flaws In Injury Prevention Programs
October 25, 2023How to Prepare for an Inspection Under OSHA’s New NEP on Warehousing and Distribution Centers Operations
On October 13, OSHA inspections are set to kick off under the National Emphasis Program (NEP) on Warehousing and Distribution Center Operations. NEPs are temporary programs that focus resources on particular hazards and high-hazard industries that OSHA feels warrant additional oversight. Currently, there are only 13 NEPs.
What employers should do now:
-
- 444110 – Home Centers
- 444130 – Hardware Stores
- 444190 – Other Building Material Dealers
- 445110 – Supermarkets and other grocery stores
- 452311 – Warehouse Clubs and Supercenters
- These establishments will have inspections of just the loading and storage areas of facilities, but inspectors can expand the scope of these partial inspections where evidence of other violations exists.Confirm your establishment is covered by the NEPNEP inspections mean OSHA can show up unannounced, even if there is no triggering event, and conduct a comprehensive (wall-to-wall) inspection. Further, should OSHA show up based on an injury, hospitalization, death, or complaint, they can use this enforcement initiative to expand the scope to a NEP inspection. The NEP does not have a threshold for the number of employees, so small businesses are included. Establishments inspected by OSHA in the last three years with an inspection focused on the same hazards covered by the NEP should be exempt.
Before allowing an inspection, employers should be sure they are covered under the NEP by checking the listed two North American Industry Classification System (NAICS) codes:
Warehousing and Distribution establishments
- 491110 – Postal Service (Processing & Distribution Centers only)
- 492110 – Couriers and Express Delivery Services
- 492210 – Local Messengers and Local Delivery
- 493110 – General Warehousing and Storage
- 493120 – Refrigerated Warehousing and Storage
- 493130 – Farm Product Warehousing and Storage
- 493190 – Other Warehousing and Storage
- These establishments will have comprehensive (wall-to-wall) inspections.
High Injury Rate Retail establishments
If an inspector shows up and you don’t agree that the establishment falls under the NEP, experts suggest not to refuse the inspection but ask to “pause” it and allow time to confirm.
- Know the focus of an inspectionAccording to Conn Maciel Carey LLP, a firm focused on Labor & Employment, and Workplace Safety, OSHA finds violations in 70 percent of inspections. Many of the hazards in warehouses are “low hanging fruit” for inspectors – easy to identify and often cited. The NEP notes, “Inspections conducted under this NEP will focus on workplace hazards common to those industries including, but not limited to, powered industrial vehicles operations, material handling/storage, walking-working surfaces, means of egress, and fire protection. Heat and ergonomic hazards shall be considered during all inspections covered by this NEP and a health inspection shall be conducted if OSHA learns that heat and/or ergonomic hazards are present.”Therefore, compliance efforts should focus on the relevant standards, including five subparts of 29 CFR 1910, as well as 29 CFR Part 1904 – Recording and Reporting Occupational Injuries and Illnesses.
- Subpart E – Exit routes and emergency planning
- Subpart D – Walking/working surfaces
- Subpart I – Personal Protective Equipment
- Subpart L – Fire protection
- Subpart N – Material handling/storage, which includes powered industrial vehicles operations
While these may be the focus of the inspection, in a recent webinar OSHA noted that several other standards can come into play during an inspection. All relevant standards can be found on the warehousing webpage.
Here are some of the most frequently cited standards* in covered industries and best practices:
Material handling and storage, such as the safe stacking of pallets and other materials Section 29 C.F.R. § 1910.176 is often cited, particularly section b – secure storage, section a – use of mechanical equipment, and section c – housekeeping. Ensure that bags, containers, bundles, etc., stored in tiers are stacked, blocked, interlocked, and limited in height so that they are stable and secure against sliding or collapse. Allow sufficient clearance for mechanical equipment throughout the warehouse and loading dock, and keep storage areas free from slip and trip hazards. It’s important to have written documentation of regular audits and walk-through observations.
Storage rack systems – General Duty Clause. The General Duty Clause is often used to cite employers for pallet racks and other types of industrial steel shelving that are not adequately secured from falling over. To avoid such citations, it’s a best practice to have a written rack inspection program, regular inspections by a trained team, documentation of repairs by a qualified contractor, visible load rating placards, and a system for employees to report concerns.
Powered industrial truck (PIT) operations, such as forklifts and other vehicles meeting the definition of a powered industrial truck (29 C.F.R. § 1910.178)
- Be sure to have an adopted and implemented written PIT operations program.
- Approximately 60 percent of all citations relate to section (l) – training, particularly sections 1(i), 1(ii), 6, 4(iii), 2(ii). Documentation of proper training, evaluation, and certification of all forklift operations is key. Be sure operators are trained on all types of equipment that they operate.
- Other common citations relate to repairs and defects, including sections p(1) and q(7). The requirement that all PITs be inspected before being placed in service is often misunderstood. Inspections are required before each shift, even if there were no issues on the prior shift.
- If attachments and/or additions are made to the equipment, having documentation from the manufacturer or an engineer that there will be no adverse effect on operations can help avoid citations. Common violations occur under sections a(4), a(5), and a(6).
- Operator violations under sections m(5)(i), n(4), n(6), and (o)(1) are also commonly cited. It’s important to issue disciplinary action for violations, document findings, retrain disciplined employees, and document retraining.
- Have a robust dock safety program with proper barriers and worker protection.
Exit routes and emergency planning (29 C.F.R. 1910.36 &1910.37). Low-hanging fruit for OSHA, these violations are easy to cite and difficult to defend. Documentation of inspections at the beginning and end of each shift can help.
- Most frequently cited are 1910.37(a)(3) – exit routes must be free and unobstructed and 1910.37(a)(2) – each exit must be clearly visible and marked by a sign reading Exit.
- Other frequently cited sections are 1910.36(d)(1) – employees must be able to always open an exit route door from the inside; 1910.37(b)(4) – signage if the direction of travel to the exit or exit discharge is not immediately apparent; and 1910.36 (g)(2) – An exit access must be at least 28 inches (71.1 cm) wide at all points.
Fire protection (29 C.F.R. 1910.157). Violations relating to portable fire extinguishers are the most frequently cited under this standard, including:
- 1910.157(c)(1) – The employer shall provide portable fire extinguishers and shall mount, locate, and identify them so that they are readily accessible to employees without subjecting the employees to possible injury.
- 1910.157(e)(2) & (e)(3) – Inspections. Fire extinguishers shall be visually inspected monthly and receive an annual maintenance check.
Walking and working surfaces. This standard is extremely broad, covering everything from housekeeping to ladders and stairs to fall protection.
- Common violations in covered industries include: 1910.22, .23, .25, .26, .28, .29, and .30.
- Maintain good housekeeping practices by ensuring floors are free from debris, water, holes, loose boards, nails, and other slip and trip hazards.
- Ensure that there is an up-to-date hazard assessment, managers and supervisors are inspecting all walking and working surfaces and conducting and documenting safety walks regularly, and train and retrain employees as necessary.
- Be sure aisles are wide enough for mechanical handling equipment.
Personal protective equipment
- Section 1910.132 is frequently cited when an employer cannot document nor provide written certification that a PPE Hazard Assessment has been completed. Violations related to eye, head, hand, foot, face, and respiratory protection, as well as personal fall protection systems, are also common.
OSHA Recordkeeping, the recording and reporting of certain types of injuries and illnesses (29 C.F.R. § 1904)
- Be prepared to provide your 300 logs, 300A summaries, and 301 forms at the beginning of the inspection. Be sure they are in good order as they must be provided within four business hours of the request. Check to identify whether any injuries or illnesses were caused by hazards covered by the NEP and verify that you have strong documentation of corrective actions.
- Common violations in covered industries include: 1904.4, .7, .29, .31, .32, 39, .40, and .41.
*Sources: OSHA, Conn Maciel Carey, JJ Keller
- Don’t forget the inspection can be expanded to heat or ergonomic hazardsThe NEP clearly states that heat and ergonomic hazards shall be considered during all inspections. If the injury and illness records, plain view hazards, employee interviews, or any other aspects of the inspection raise red flags, inspectors will expand the scope of the inspection.There is a NEP on Outdoor and Indoor Related Heat hazards.
While there is no standard or NEP for ergonomics, citations are issued under the General Duty Clause, which states that employers must keep their workplaces free from recognized serious hazards, including ergonomic hazards. For more information.
- State OSHA plans may have different regulationsEach state-plan state must adopt an emphasis program that is identical to or at least as effective as the federal OSHA NEP. In September, the plans had to notify OSHA of their intent to either adopt the federal plan or create their own. For more information, contact the state plan.
For additional information: OSHA NEP Warehouse Webinar slides or schedule a meeting with one of our professionals today.