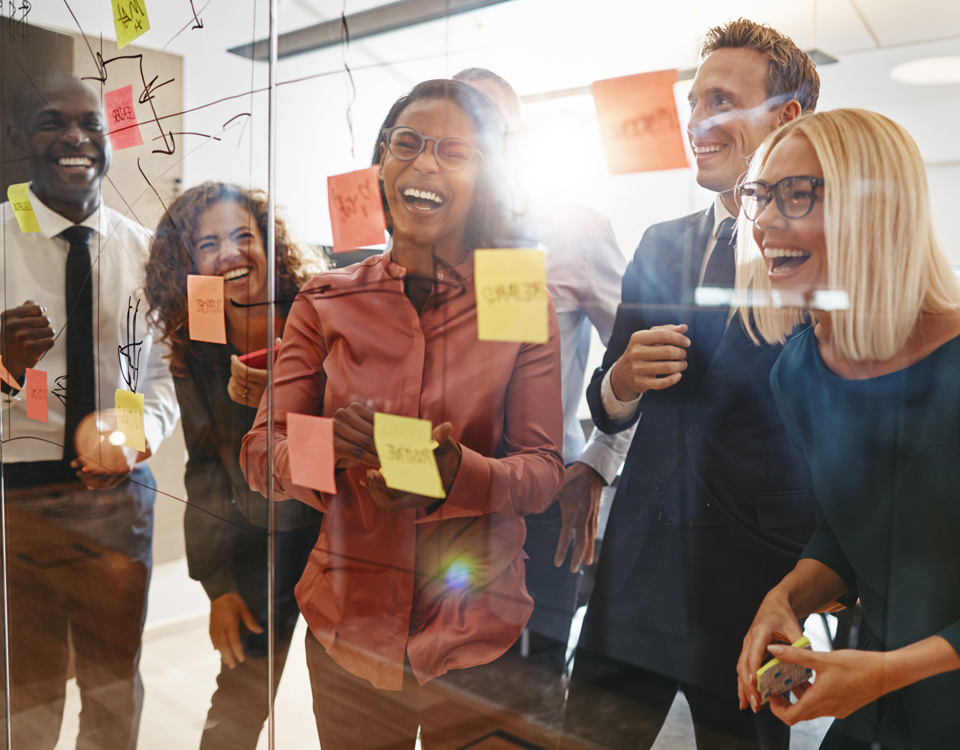
The evolving nature of workplace wellness: five keys to a healthy workforce
March 9, 2022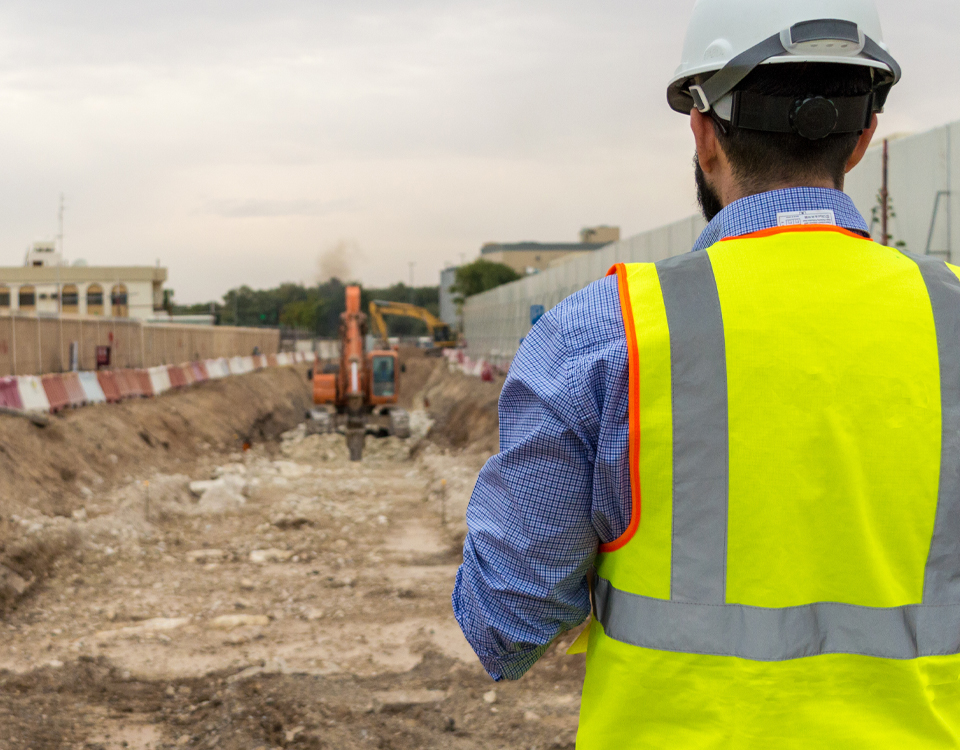
Lessons from America’s safest companies
March 9, 2022When it comes to protecting your employees don’t let the dominoes fall where they may
We’ve all seen those images of dominoes lined up in a row. Could be 5,10, maybe even 1,000s. Then someone flicks the first one gently and suddenly a cascade unfolds as one domino falls against the one beside it, knocking them all over. It’s awesome to watch, but it takes precision in setting them up so they fall just right. Too close together and they don’t fall correctly; spaced too far apart and one falls without hitting the others. Still, it’s really all cause and effect.
So how does this equate with job safety? The answer: accidents don’t happen in a vacuum. Most times when there is an injury in the workplace it can be traced back to something that happened (or didn’t happen) that resulted in somebody being injured. But back to our domino analogy.
Let’s say there are five dominoes lined up. If you removed, say, domino number three and then flicked domino number one, what happens? Domino number one and number two fall, but because you removed domino number three, numbers four and five remain standing. You have stopped a chain reaction by removing something (number three) that would have caused an effect (all five dominoes falling).
So, what we are saying is, when something bad happens in the workplace chances are if you truly retrace how it happens-the circumstances that led up to it-you will most often find that you could have prevented it by removing a “domino.”
When we first meet employers to help them improve safety and operations, reduce their costs and premiums, we routinely review accident investigations of injuries to see what is causing injuries and accidents and then make recommendations as to how to address things moving forward. Without a doubt, 80-90% of the time when we review accident investigation forms we see the Root Cause as “Employee did not follow procedures”, “Employee created shortcut”, “Employee…”, etc., followed by the Corrective Action of “Employee needs more training.”
However, when we truly start to dig in and ask more questions, interview witnesses and people involved, the picture changes. In essence, take this dominoes theory-but in reverse.
All the dominoes are set up, nice and neat, ready to tumble:
An employee’s first daily job is to blow excess varnish off the metal-air filter in the spray booth using an air compressor hose and then clean up the residue.
Domino #1-The employee did not ground himself.
Domino #2-There was a static discharge from the air hose nozzle that ignited varnish flakes.
Domino #3-There was no fire extinguisher in the spray booth.
Domino #4-Because there was no fire extinguisher in the booth, the employee had to go outside thus leaving the door open.
Domino #5- The chemical foam fire suppression system wasn’t properly maintained by the service contractor, improperly discharging on the far end of the booth only, blowing burning flakes into the shop.
Domino #6- The open door allowed the sparks to be sucked into the dust collection system.
Domino #7- A leaking connection in the dust collection pipe in the concealed attic space allowed some burning flakes into the attic and ignited the layer of sawdust.
Domino #8-The building burns down – putting a company out of business for almost a year.
What happens if we eliminate domino #3 because now there is a fire extinguisher in the spray booth? Now the employee doesn’t have to open the door and dominoes #4, #5, #6, and most importantly, #8 never happen. By eliminating a cause, you have curtailed an effect.
If in #5, the service contractor did not take a shortcut and just tag the system but followed protocol and tested if there was an issue, the entire system would have discharged probably stopping the fire in the booth.
If #7 was eliminated through routine attic inspections, the only fire would have been in the dust collection system outside, only requiring a few days to be repaired/replaced.
Okay, let’s see how this domino theory holds up against an injury on the job:
Domino #1-An employee using a band saw doesn’t put down the protective blade guide because he is cutting different thicknesses of material. And by not putting down the guide he can cut faster.
Domino #2-Cutting without a blade guide causes the blade to wobble.
Domino #3-The boss approaches and begins talking to the employee while he’s cutting, causing a distraction.
Domino #4-The boss allows the employee to keep working while asking questions or tells the employee to keep working (stories differ).
Domino #5-The boss allows the employee to not use the protective blade guide “because it is more productive.”
Domino #6-The boss does not address the use of a blade guide even though the employee and prior employees have broken blades due to wobbling.
Domino #7-Everyone is failing to follow the procedure.
Domino #8-There doesn’t seem to be the need to properly train the employee, therefore, the employee just follows the bad example of the previous user who trained him before moving onto a new area of the shop to work.
Domino #9- The boss then asks a question that requires the employee to look at what the boss is pointing at, turning his head and shoulders while cutting.
Domino #10-Goodbye to two of the employee’s fingers.
How could we have avoided this horrible accident? The obvious solution rests in eliminating domino #5 from the lineup, where it is obvious the company put productivity (i.e., speed) above the safety of its employees. But eliminating any other prior step would have stopped the dominoes from falling. For this company, it was all about getting from point A to point B as directly, and quickly, as possible. There was never a thought that the quickest way might not be the right away.
An example: the GPS in your fully loaded delivery truck might say the “quickest way” to get across town is to take a direct route. But what if that direct route takes you over a river by way of an older, weight-restricted bridge that might collapse? Sure, it’s the shortest route, but is it the best route. Is it better than the one that takes you a few minutes out of your way but gets you safely to where you want to go?
When setting up a risk prevention program, the smart move is to see every possible hazard as those dominoes lined up on a table, and where you can remove the domino-or dominoes needed to prevent that hazard from happening.