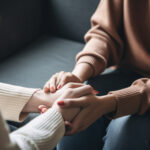
How Two Organizations Reduced Claims through Mental Health Services and Support
October 5, 2023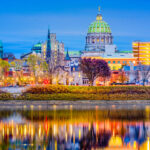
Rating bureau news: Pennsylvania, NCCI
October 5, 2023Understanding the Drivers of Serious Injuries by Industry
2023 Liberty Mutual Workplace Safety Index
Produced annually, the Liberty Mutual Workplace Safety Index identifies the leading causes of the most disabling non-fatal workplace injuries (resulting in more than five days of lost time) and ranks them by direct Workers’ Compensation costs, including medical and lost-wage payments. It provides insight into critical risk areas, helping businesses to better allocate safety resources by identifying the causes and costs of the most serious workplace injuries in eight industries.
Workplace injuries cost employers more than $58 billion in annual medical costs and lost wage payments with the top 10 causes of injuries and illnesses accounting for over 82 percent ($48.2 billion), according to the report that is based on 2020 data from Liberty Mutual, the U.S. Bureau of Labor Statistics, and the National Academy of Social Insurance.
While overexertion, slips, trips, and falls remain consistently at the top of the list, exposure to other harmful substances and pedestrian vehicular accidents joined the index for the first time in 2023. COVID-19 was a contributor to both these factors. Without the effects of the pandemic, exposure to other harmful substances would have ranked 18th. A news release states, “Pedestrian vehicular incidents were most evident in occupations such as sales and truck drivers, material movers, food service, distribution managers, retail salespersons, building cleaning and maintenance, and protective service. These occupations were likely to be impacted by the challenges that COVID-19 placed on the U.S. supply chain, as well as on industrial hygiene, security, and novel delivery or parking-lot operations.” With the addition of exposure to other harmful substances and pedestrian vehicular incidents, traditional top-10 causes of loss – struck against object, or equipment and repetitive motions involving microtasks – fell out of the top ranking.
Here are the top ten causes, the costs, and some common preventive steps:
- Overexertion involving outside sources, such as lifting, pushing, carrying heavy objects: $12.84 billionAction steps: Utilize equipment to reduce need to lift heavy items,store materials close to work area, train employees on proper ways to perform physical tasks, schedule breaks
- Falls on the same level, such as slips on wet floors: $8.98 billionAction steps: Consistent good housekeeping practices, robust maintenance of all walking surfaces, non-slip mats and flooring, train workers on proper cleanup, proper lighting, caution signage
- Falls to lower level, such as improper ladder use: $6.09 billionAction steps: Minimize the use of ladders, proper fall prevention systems, PPE, and training, engineering controls, balanced loads
- Struck by object or equipment, including unsecured objects stored above: $5.14 billionAction steps: Ensure functional and safe storage of all workplace supplies and products, ensure racks are properly designed and installed, use PPE (hard hats) when needed
- Other exertions or bodily reactions from activities, such as awkward positions, bending, twisting, stepping down from vehicle: $3.67 billionAction steps: Workplace risk assessments, wearables, ergonomic measures
- Exposure to other harmful substances, such as close quarters spreading communicable diseases: $3.35 billionAction steps: Programs for ventilation, surface cleaning, scheduling, and PPE
- Roadway incidents involving motorized land vehicle, often caused by distracted driving: $2.58 billionAction steps: Safe driving policies and continuous training, distracted driving reminders
- Caught in or compressed by equipment or objects, including moving or rotating machines or equipment: $1.98 billionAction steps: Properly staff and supervise shifts, provide protective barriers, proper machine guarding, train employees
- Slip or trip without fall, such as slippery or uneven walkways: $1.92 billionAction steps: Promptly address weather-related hazards, maintain all walkways, no-slip rugs at entrances and exits, keep workspaces tidy
- Pedestrian vehicular incidents, often caused by rushed behaviors, inadequate scheduling times: $1.61 billionAction steps: Allow adequate time for employees to complete tasks without rushing
Even when broken down by eight industry sectors, there was consistency with overexertion and falls on the same level in the top five causes for each of the sectors. Here are the industry results:
Construction – $11.4 billion in losses
- Falls to a lower level: $3.22 billion
- Overexertion involving outside sources: $2.09 billion
- Struck by object or equipment: $1.52 billion
- Falls on the same level: $1.0 billion
- Other exertions or bodily reactions: $0.86 billion
Manufacturing – $8.32 billion in losses
- Overexertion involving outside sources: $1.80 billion
- Falls on the same level: $1.20 billion
- Struck by object or equipment: $0.97 billion
- Caught in or compressed by equipment or object: $0.82 billion
- Falls to a lower level: $0.71 billion
Professional and business services – $8.08 billion in losses
- Falls on the same level: $1.73 billion
- Overexertion involving outside sources: $1.56 billion
- Falls to a lower level: $1.07 billion
- Struck by object or equipment: $0.60 billion
- Roadway incidents involving motorized land vehicle: $0.47 billion
Health care and social assistance – $5.56 billion in losses
- Overexertion involving outside sources: $1.54 billion
- Falls on the same level: $1.35 billion
- Exposure to other harmful substances: $0.50 billion (includes COVID-19)
- Intentional injury by person: $0.37 billion (workplace violence)
- Other exertions or bodily reactions: $0.29 billion
Retail – $5.39 billion in losses
- Overexertion involving outside sources: $1.64 billion
- Falls on the same level: $1.08 billion
- Struck by object or equipment: $0.55 billion
- Falls to a lower level: $0.41 billion
- Other exertions or bodily reactions: $0.36 billion
Transportation and warehousing – $4.79 billion in losses
- Overexertion involving outside sources: $1.37 billion
- Falls on the same level: $0.63 billion
- Other exertions or bodily reactions: $0.46 billion
- Falls to a lower level: $0.44 billion
- Roadway incidents involving motorized land vehicle: $0.40 billion
Wholesale – $4.19 billion in losses
- Overexertion involving outside sources: $1.32 billion
- Falls to a lower level: $0.53 billion
- Falls on the same level: $0.52 billion
- Struck by object or equipment: $0.34 billion
- Other exertions or bodily reactions: $0.27 billion
Leisure and hospitality – $3.35 billion in losses
- Falls on the same level: $1.22 billion
- Overexertion involving outside sources: $0.43 billion
- Struck by object or equipment: $0.28 billion
- Other exertions or bodily reactions: $0.25 billion
- Falls to a lower level: $0.24 billion
While overexertion ranked first for five of the eight industries and was second for the remaining three, other loss causes are often industry unique. For example, manufacturing was the only industry to include caught in or compressed by equipment or object, intentional injury by person was unique to health care and social assistance, and falls to a lower level topped the construction list.
Industry-wide data is best used as a supplement to a company’s data and analytics. Employers can use the data to develop preventative safety interventions for job duties or machines prone to causing injuries. Although risk is a part of doing business, understanding the risk and having controls in place is the best way to prevent injuries and improve the bottom line.
To discuss this more, schedule a meeting with one of our professionals today.